Processes related with logistic enterprises are known to be some of the most difficult to monitor due to the number of elements that must be watched, their geographic movements and the different statuses or stages the different elements go through.
With Pandora FMS weโve faced monitoring various logistic processes and have acquired a large amount of experience on necessary KPIs which are really useful in logistics. Weโre conscious of the fact that each logistic process has its own characteristics and must apply different particularities for its monitoring. But, we also know that some processes donโt even have basic KPIs under monitoring. For this reason, through this brief article, we want to give the main hues so you can know the main KPIs to measure in your logistics process.
KPIs and logistics, a success case
Thanks to our experience of working with various logistics companies, we have compiled a list of the most important KPIs related to the sector. The following is a detailed look at the principal KPIs employed in the logistics sector, but first letโs take a look at how monitoring can be an invaluable support, and entail a cost reduction, for logistics companies, leading to an increase in client and user satisfaction.
Check real success stories in the Logistics Industry
Why KPIs are so important to the logistics sector
Being able to measure your companyโs performance using indicators gives you a comprehensive view of said metric. KPIs permit for the setting of objectives, which can grow in scale and ambition as they are fulfilled.
We hope that you will find the following information useful. Donโt hesitate to chip in with your own thoughts about the usefulness and the principal features of KPIs as they relate to logistics.
KPI goals in logistics and their processes
Before we begin to talk about the main indicators in logistics, we should know the main objectives behind monitoring these:
- Improving the quality of our process, diminishing mistakes.
- Optimizing costs, therefore raising company benefits.
- Improving performance and productivity.
- Having a real-time view of our business and being able to predict possible issues as soon as possible.
Basic processes for a logistic enterprise
From de point of view of a logistics process we could, with an overview, divide the process into the following stages:
- Provisioning: the moment at which logistic companies pick up those products meant for distribution.
- Storage: due to the fact that on many occasions companies donโt sell previously stocked products immediately, it becomes a necessity to store acquired products during some time.
- Order preparation: once a sales order reaches the warehouse, the next step should be to prepare the order for shipping. Lately, companies are competing in this stage in order to try and optimize time dedicated to this phase.
- Distribution: once the product has been prepared, the distribution stage may begin. This can carry as many trips and purveyors as the physical distance to reach the customer requires.
- Inverse logistics or refund processes: we mustnโt forget those occasions on which products are returned, and this must be a monitored part of the process as well.
Main KPIs or logistics indicators to keep in mind
Up next weโll list the main logistic KPIs to keep track of during each stage:
KPIs during storage and order preparation
Inventory: we must have our warehouse stock and remaining units perfectly inventoried. Along with each product we must have the weight and dimensions it has in order to further optimize the transport process. Itโs vital to have that information and thus be able to estimate a continuous product delivery for our customers.
Time lapse from product reception to sending: itโs important we measure that KPI and that we know the percentage of deliveries that surpass the established average time. Thisโll give us a lot of important information on the need that our customer shows for said product.
Itโll be important to know our maximum storage capacity and the current status of this, to be able to detect refund saturation in the warehouse.
Order preparation duration. Itโll be important to know how much time different orders take to package and ship, in order to detect which ones are slower and in general cause tardiness, and create measures to optimize the process.
Number of orders packaged and sent per worker. Thisโll allow us to know the performance our warehouse provides.
Product storage costs. Itโll be important to know the cost that a warehouse, and its corresponding maintenance tasks, implies for the company. Knowing this number will allow us to better know the cost for each of our stored products and which is the optimal status in the inventory to optimize these expenses.
KPIs in Distribution
Delivery time, which is the time range from when the customer places a shopping order until he or she finally receives it. On this particular occasion itโll be of prime importance to segment distribution and identify the main participants in distribution, in order to be able to measure them individually.
If multiple purveyors participate in the distribution, we should identify at which point each one begins and finishes, and try to measure the time that each of them takes. In case a distribution process uses multiple means of transportation, itโll be very important to measure each means of transportation and time elapsed between the point of origin and final destination.
Cost per kilo (or lbs.). We should obtain the cost for each order, along with the weight said order has. This KPI will be vital in logistic processes in order to estimate future shipping and be able to save costs when placing orders.
With these pieces of data, we can know the optimal size for our orders, thus being able to, along with our shipping times, manage our shipping in a more efficient way.
Itโs important to keep in mind that, not only must the number of orders shipped be measured, but that also from the total we have to know which one have been correctly delivered, and which have had issues upon delivery. Deliveries must be measured not only in quantity, but also in quality. We must be able to see the quality indexes further along.
Inverse logistic KPIs
Itโll be very important to know the percentage of products that require an inverse logistics process, and the reasons motivating each one. The objective of measuring these numbers is to obtain the quality of our deliveries and to be able to detect possible improvements in the system, as soon as possible.
We should also bear in mind the same KPIs as the distribution process, but in this case theyโll be measured by the refund process.
Quality indicators in logistics
As we mentioned earlier, not only must we measure the number of orders and their delivery times, we also have to know the quality in their delivery. As a general statement, we must be able to identify and measure the quality of our service and for this we need to be able to obtain the following metrics from our logistics process:
- Percentage of faulty products delivered.
- Percentage of issues caused during each step in the process.
- Percentage of correctly delivered orders.
Itโll also be recommendable to evaluate the opinions of our final customers and include them in our KPIs in order to know the quality of our final delivery.
In this article weโve talked about the main elements we need to measure and keep in mind in order to know the general status of our logistics process. We know that each case has its particularities, and therefore must be studied using the solution that best fits your needs as a company, but we hope that this article has inspired you to work on improving your logistic processes.
Do you have any experience monitoring logistics and want to let us know? What about doubts on how to get started? Donโt hesitate to let us know with your comments, weโre glad to hear from you!
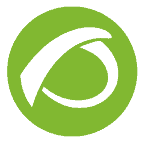
Pandora FMSโs editorial team is made up of a group of writers and IT professionals with one thing in common: their passion for computer system monitoring. Pandora FMSโs editorial team is made up of a group of writers and IT professionals with one thing in common: their passion for computer system monitoring.